Beitrag von Peter Horn, Februar 2018
Die Geschichte beginnt mit Fritz Meyerhold, er war Rektor in Lägerdorf. 1948 baute er sich einen Blitz-Jollenkreuzer und machte damit, einschließlich seiner 4 Kinder, ausgedehnte Törns bis nach Holland und Dänemark.
Nach der Wettfahrt „Blaue Band“ 1956, bei der einige Jollenkreuzer kenterten und der Tod von Elmshorner Seglern zu beklagen war, wuchs die Erkenntnis, dass Jollenkreuzer für die offene See nicht geeignet sind.
1953 hatte Theodor Stölken einen eisernen 6 KR Kielschwerter entworfen. Das Schiff traf den Geschmack vieler Segler und es entstand die Einheitsklasse Delphin.
Fritz Meyerhold kaufte die Lizenz für den Eisendelphin, und es entstand in Eigenarbeit und mit Unterstützung erfahrener Bootsbauer der eiserne Delphin 22. Mein Freund Hobe Hein und ich segelten schon viele Jahre mit einem 7m Kielboot meiner Eltern in unseren Gewässern. Während der Bauzeit des Eisendelphins segelten die Meyerhold-Kinder häufig mit uns.
1959 ging der Eisendelphin zu Wasser und wir sammelten in unterschiedlicher Besetzung auf vielen Törns Erfahrungen mit dem Schiff. Die Reisen führten uns u.a. nach Norwegen und zu den Aalandinseln.
1965 verkaufte die Gemeinde Lägerdorf überraschend das Schulgebäude, in dem Fritz Meyerhold wohnte, und er musste schnell Geld beschaffen, um nicht ausziehen zu müssen. Er verkaufte daher den Delphin 22 nach Stade.
Hobe und ich waren dabei unsere Ausbildung zu beenden. Da unser Boot schon recht betagt war, schauten wir uns nach etwas Größerem um. Hobe hatte die Tochter von Fritz geheiratet und so wurden wir zu einem Verband, der 3 Schiffe suchte. Wir Jungen suchten natürlich nach etwas Schnellem. Fritz suchte dagegen, da er die Kinder nicht mehr einplanen musste, nach etwas Kleinerem.
Der Markt für gebrauchte Boote war damals schlecht bestückt, daher kam nur der Selbstbau in Frage. Selbstbau war damals, im Gegensatz zu heute, etwas Übliches.
Heiße Diskussionen ergaben sich aus der Werkstofffrage. Diskutiert wurden:
- Eisen
- Holz (geplankt)
- Holz (formverleimt)
- Sperrholz
- Glasfaserverstärkter Kunststoff
Eisenschiffe waren uns im Selbstbau meistens zu beulig. Für den Bau von Holzschiffen mangelte es uns an Erfahrung. Sperrholz kam für uns nicht in Frage, weil wir Knickspanter nicht leiden mochten. GFK erschien uns für unsere Fähigkeiten der einzig vernünftige Weg.
Eine Anfrage beim Konstruktionsbüro „van de Stadt“ nach einem Linienriss für ein GFK Boot ergab die Antwort: „GFK ist für den Selbstbau nicht geeignet“ und die Zusendung einiger Prospekte für Knickspanter.
Ein Gespräch mit Paul Böhling, einem damals sehr renommiertem Konstrukteur, ergab die Antwort: „Für Kunststoff gebe ich meinen Namen nicht her.“
Da wir mit einer Bauzeit von mindestens 3 Jahren rechnen mussten, auch schon aus finanziellen Gründen, wurde uns klar, dass wir nicht nach dem aktuell am schnellsten aussehenden Riss suchen durften, denn der wäre in 3 Jahren ohnehin überholt, sondern nach einem soliden, zeitlosen Schiff.
Unsere Kontaktaufnahme mit Theodor Stölken, dem Konstrukteur des Eisendelphins, ergab anfangs wenig Begeisterung seinerseits. Erst als wir erklärten, dass wir 3 Schiffe bauen wollten und wir nur einen Generalplan und einen Linienriss brauchten, stimmte er zu. Zur Frage der Bootsgröße erklärte er ganz trocken: „Unterhalb der Delphingröße würde er nichts machen, da könnte kein vernünftiger Entwurf entstehen.“
Damit war die Schiffsgröße entschieden und wir konnten die Details festlegen. Unsere Wünsche waren:
- schärferes Vorschiff
- größere Breite weiter achtern
- Volumenschwerpunkt weiter achtern
- Tiefgang max. 1,05
- Schwert unterhalb des Fußboden
- kein freistehendes Ruder
- senkrechte Ruderachse
- senkrechter Spiegel
- größerer Freibord
Unsere Wünsche wurden von Theodor Stölken
als richtig empfunden und akzeptiert. Bis auf den Unterwasserhauptspant blieb kein Spant vom Eisendelphin erhalten. Im Frühsommer 1966, wir Jungen waren in das Berufsleben eingetreten, begannen wir unsere Werkstatt zu bauen, in der Platz war für:
- die liegenden Formhälften, bzw. 1 Schiff
- die Polyesterharz Lagerung, Zubereitung und die
- Werkzeugreinigung
- die Glasfaser Lagerung und Zubereitung
- die Heizung zum Tempern der GFK Bauteile
- die Absaugung der Styroldämpfe
- die Werkbank
Rechtzeitig erhielten wir von Theodor Stölken:
- den Generalplan
- den Linienriss
- die Aufmaßtabelle
Nun konnten wir loslegen. Mit Hilfe der Aufmaßtabelle wurde der Spantenriss im Maßstab 1:1 auf eine Hartfaserplatte aufgetragen und diente als Vorlage für die Herstellung der 10 Spanten und Hilfsspanten.
Die Spanten wurden auf das erforderliche Maß gesägt und auf die Helling gestellt.
Das Spantgerüst wurde mit gleichmäßig dicken Leisten beplankt.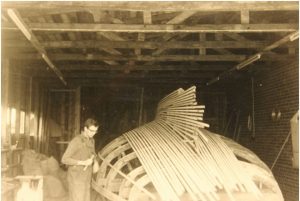
Der beplankte Rumpf wurde, um eine gute Haftung mit der Gipsschicht zu bekommen, mit Jutesäcken und Drahtgewebe verstärkt.
Anschließend wurden in gleichmäßigen Abständen Hilfsleisten angebracht, die für eine gleichmäßig dicke Gipsschicht sorgen sollten.
Nachdem der Rumpf mit Gips überzogen war, wurden die 10 mm dicken Hilfsleisten herausgezogen und der Leerraum auch mit Gips aufgefüllt. Nun begann das mühevolle Glätten der Gipsoberfläche.
Auf dem Bild seht ihr Fritz mit einem ca. ½ m langem Schleifbrett für Übergänge und Ecken. Die Hauptarbeit erfolgte mit
einem 2,5 m langen Sperrholzbrett auf dem Schmirgelpapier aufgeklebt wurde. Das Brett hatte vier Griffleisten. Zwei Mann konnten nun den Rumpf strakend schleifen.
Fehlstellen wurden sichtbar gemacht, neu aufgespachtelt und wieder geschliffen.
Während dieser Arbeit erhielten wir Besuch vom Konstrukteur Theodor Stölken.
Er war mit unserer Arbeit einverstanden. Hobe war an diesem Tag leider auf Dienstreise. Nachdem wir die Gipsoberfläche für gut gefunden hatten, wurde der Rumpf mit vielen Lagen lackiert.
Um die Form teilbar zu machen, wurde über die ganze Länge des Rumpfes, eine Trennwand montiert gegen die die Formhälfte laminiert wurde.
Nachdem die Formhälften fertig laminiert und mit Versteifungen und Stützen versehen waren, konnte die Form vom Kern abgenommen werden.
Die Rumpfform wurde im Garten gelagert und der Formenkern konnte verschrottet werden.
Nach gleicher Methode, jedoch mit mehr ebenen Flächen, wurde der Deckskern hergestellt. Nachdem die Decksform lackiert und das Riffelmuster aufgeklebt war, konnte die Negativform abgenommen werden. Vorsichtshalber legten wir die Decksform auf die Rumpfform um uns zu vergewissern, ob alles zusammen passt. Wir waren mit dem Ergebnis zufrieden.
Bei solchen Arbeiten erfuhren wir viel Hilfe von Vereinskameraden, denn das Entformen und transportieren konnten wir nur von Hand machen.
Rat bei manchen Fragen erfuhren wir von Willi Asmus aus Glückstadt. Als er uns einmal besuchte, fand er unsere Fortschritte und Ergebnisse o.k. Zum Schiff meinte er:
„En Schnellläuper ward dat wol nicht, aber en godes Seeschipp“
Wir waren mit der Aussage zufrieden, denn das war ja auch unser Ziel. Die Herstellung der Schiffe ähnelte den Arbeiten, die wir im vergangenen Jahr von Jörn Götte erfahren haben und sollen deshalb nicht wiederholt werden.
1970 nach 4-jähriger Bauzeit konnten wir die Boote ins Wasser bringen. Die Zeit setzte sich zusammen aus:
- ca. 1 Jahr für Formenbau
- ca. 1 Jahr für Rumpf und Deck
- ca. 2 Jahre für Innenausbau, Holzarbeiten an Deck , Metall,-und Malerarbeiten, Masten und Bäume
Ursprünglich hatten wir 3 Jahre angenommen, aber im Laufe der Zeit steigerten sich unsere Qualitätsansprüche.
Insgesamt kamen wir auf 1/3 der Kosten von vergleichbaren Schiffen, die auf der Bootsausstellung angeboten wurden. Die Bauzeit verlief immer in angenehmer Atmosphäre, unsere Frauen haben sich gut geschlagen und wesentlich zum Ergebnis beigetragen.